O processo de fundição consiste em um molde no qual o material fundido (chamado de fundente) flui, e ao ser resfriado adota a forma do molde em questão. Neste sentido, é necessário que este material seja impulsionado por uma força, podendo ser pela força da gravidade, força mecânica ou até mesmo força centrífuga (em casos específicos). Vale ressaltar que o tipo de força influencia na qualidade do produto final.
Alguns livros antigos diziam ser possível fundir apenas metais, mas hoje podemos fundir outros tipos de materiais como: cerâmica, vidros e polímeros. Fica evidente que para fundir polímeros o processo é diferente, sendo necessário utilizar outros processos como extrusão ou injeção.
As vantagens em utilizar o processo de fundição são: gerar uma peça com uma geometria complexa, facilitar a produção seriada e baratear os custos de produção em larga escala. Em segundo lugar, vale mencionar que diversas máquinas são produzidas através deste processo.
Para realizar o processo de fundição é necessário fazer a escolha do molde, sendo possível escolher entre dois tipos: os moldes perecíveis e não-perecíveis. Sendo o perecível feito na maior parte de areia e o não perecível de metal.
O Molde
Os moldes de areia são feitos com um tipo especial de areia, chamada areia verde, que é composta por um mineral refratário granular e preparada com uma mistura de argila de bentonita e água, podendo ser acrescentados aditivos. Quando os grãos refratários são compactados em volta do modelo (o modelo é uma peça de madeira ou outro material que é igual a peça final), eles são mantidos juntos pela argila e água que juntas fazem o papel de uma cola ou liga. Quando o modelo é removido, a cavidade do molde retém o formato das superfícies do modelo.
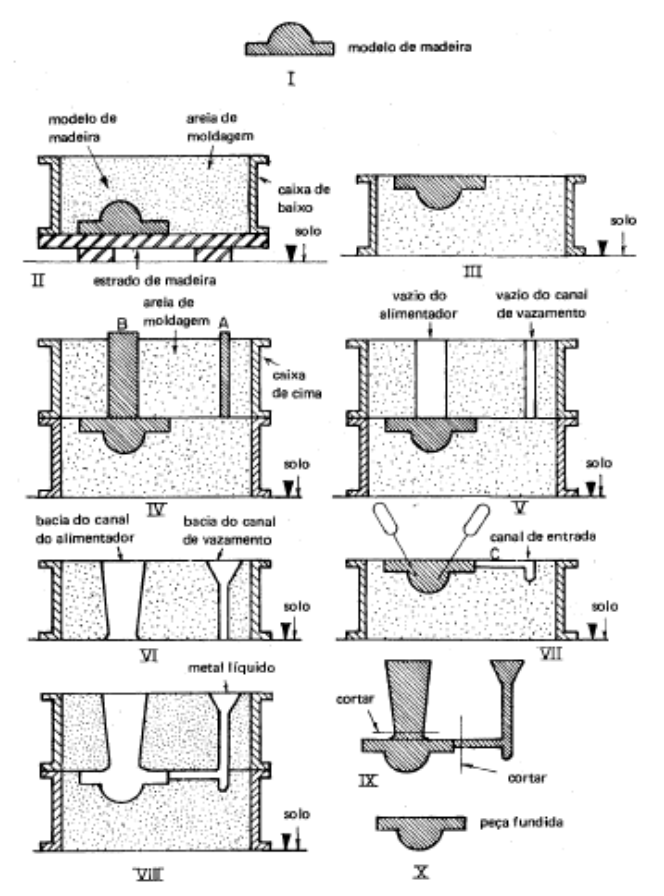
Sobre a anatomia do molde, há um funil de vazamento, o qual é utilizado para colocar o fundente dentro do molde. Ele é cortado após o término do processo. Também é importante apontar a necessidade de um massalote, que é uma cavidade dentro do molde para colocar material extra, pois à medida que o metal esfria, ele se contrai, sendo necessário para evitar falhas no produto final. Com o intuito de fazer furos na peça, podemos colocar machos, que são na maior parte das vezes cilindros que, após serem retirados, deixam um furo na peça (como mostra a imagem abaixo).
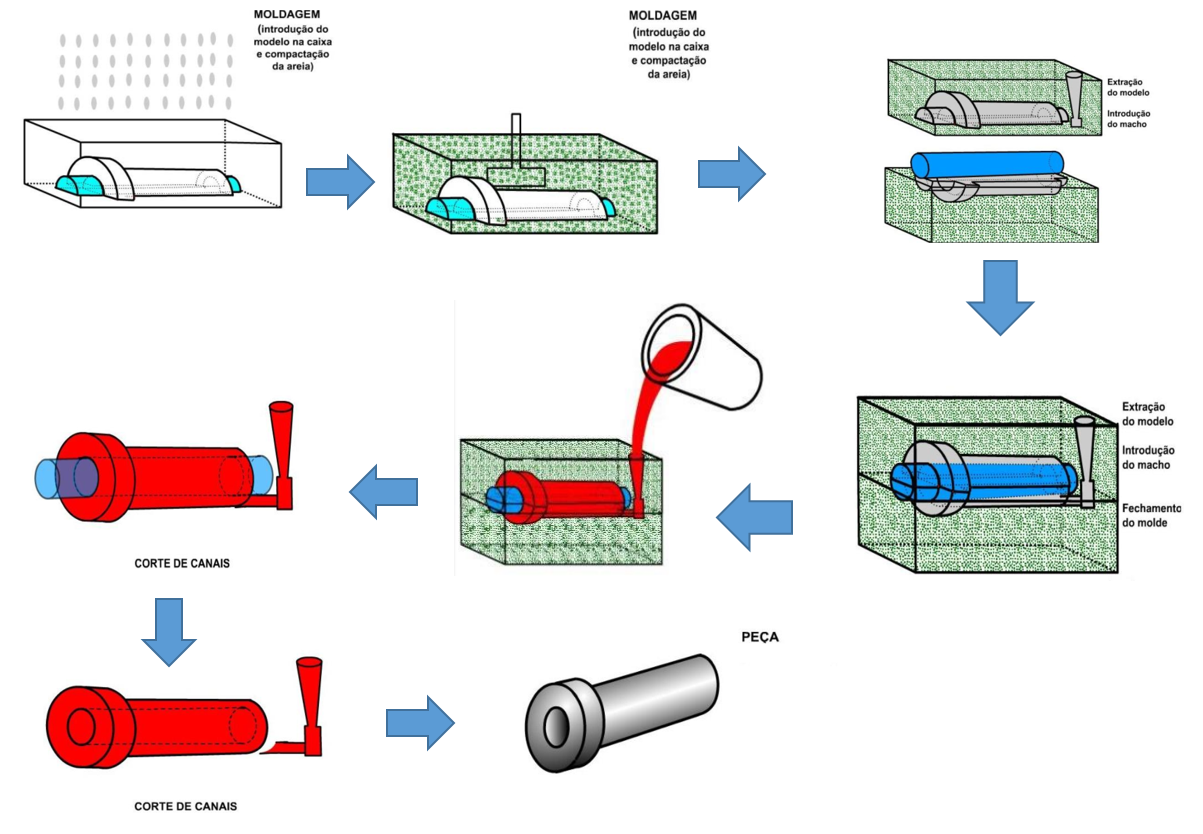
Ao fazer o molde, é necessário que a areia utilizada esteja compactada e endurecida. Há algumas formas de fazer isso, como por vibração, compressão, ou apenas deixar que o peso do excesso de material possa compactar a própria areia. Há também outra forma de endurecer a areia no molde, chamado de processo de CO2, que é uma aplicação relativamente recente. No processo, os moldes são do mesmo tipo mostrado, de areia aglomerada com silicato de sódio. Depois de compactados, eles são submetidos a um tratamento com CO2, que consiste na passagem de uma corrente desse gás através de uma seção. Ocorre uma reação entre o CO2 e o silicato de sódio; forma-se sílica-gel, carbonato de sódio e água, resultando em um endurecimento do molde em tempo relativamente curto. Não há necessidade de estufagem, alcançando-se elevadas propriedades de dureza e resistência.
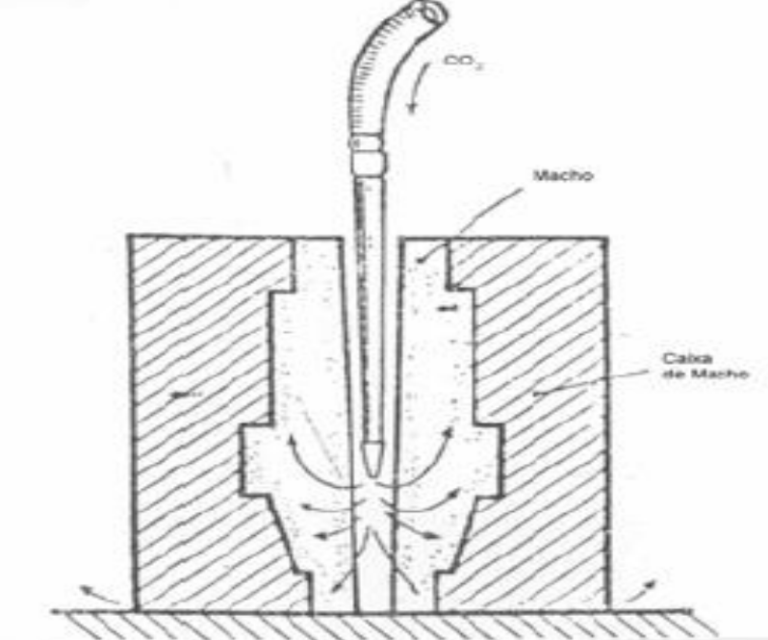
Problemas que Ocorrem no Processo
Após feito o molde e colado o fundente dentro dele, ele irá se solidificar. Porém, ao passar do estado líquido para o sólido o metal irá se contrair, gerando falhas na sua estrutura. Há um espaço vazio chamado de “chupagem” e a contração que dá origem a essa heterogeneidade é conhecida como “rechupe”. Contudo, esses vazios que ficam localizados no interior da peça (próximo a superfície, porém invisível externamente) podem ser controlados ou eliminados utilizando recursos adequados (a figura abaixo mostra um desenho de como é a “chupagem”).
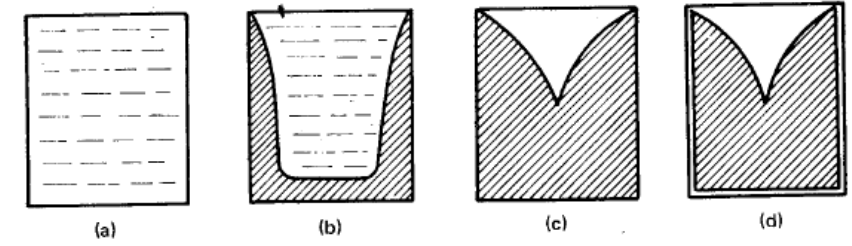
Para controlar esse efeito é colocado sobre o topo uma peça postiça de material refratário (massalote ou cabeça quente). Essa peça de material refratário retém o calor por mais tempo, e assim corresponderá à seção que solidificará por último.
Ainda durante a fundição podem acontecer outros problemas como: trincas a quente, tensões residuais, acúmulo de gases que geram bolhas, segregação do material ou mau enchimento. Ainda assim, há diversas formas de controlar estes problemas como: controlar o resfriamento, tratamento térmico para eliminar tensões residuais, projeto adequado para a peça e a adição de um reagente para eliminar as bolhas.
Ficou interessado(a)? Gostaria de saber mais a respeito de fundição e desenvolvimento de produto? Entre em contato com a OTMZA! Estamos sempre à disposição e interessados na sua ideia.